Mr. Taleb Ahmed TAGHY, Director General of SOGETRAP (Port Labour Management Company), presents his vision to address the issue: How to strengthen the efficiency of docker workforce management within SOGETRAP to contribute to the overall performance of the
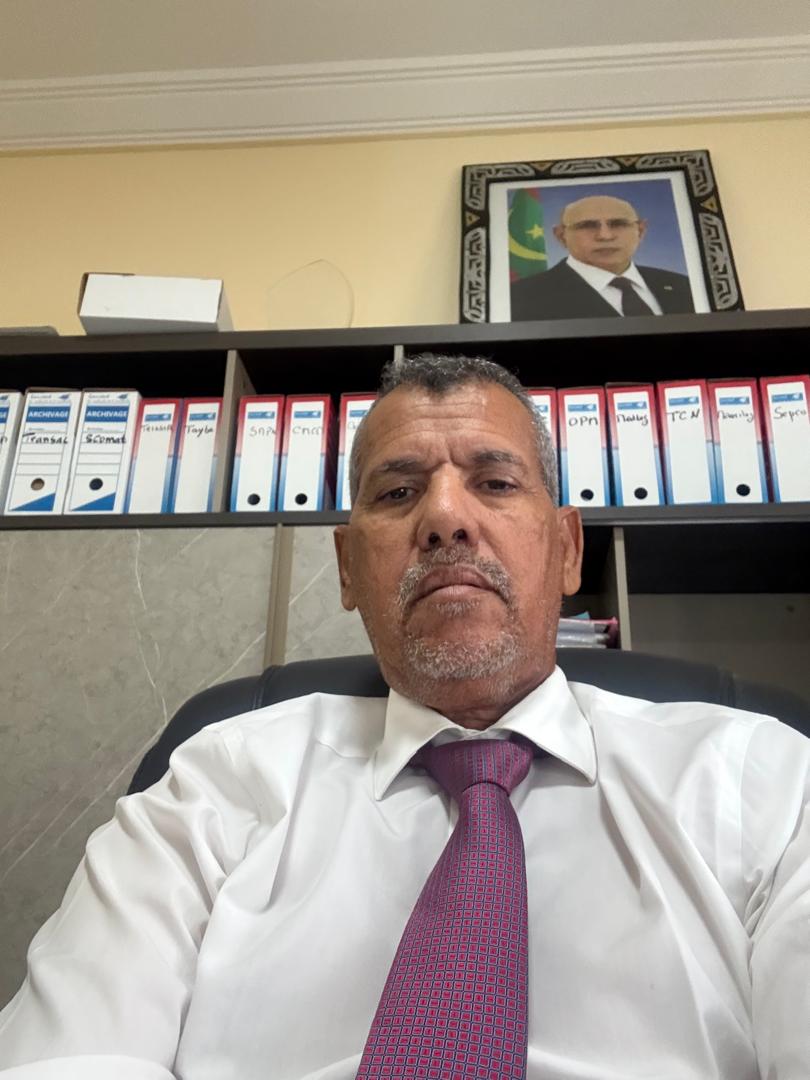
The port sector plays a strategic role in Mauritania’s economic and commercial development. Through the Autonomous Port of Nouakchott, known as the Friendship Port, the country secures the bulk of its maritime trade, notably the import of consumer goods, construction materials, and fuel. In this context, the proper functioning of the port relies heavily on the efficiency of port labour, of which the workforce is a vital link.
The management of this workforce is handled by SOGETRAP, which is responsible for the registration, allocation, and monitoring of dock workers involved in handling operations. However, despite its importance, the management system showed several limitations: manual assignments, planning conflicts, lack of a reliable database, low training levels among dockers, and the absence of effective motivation mechanisms.
In an increasingly competitive port environment, marked by infrastructure modernization and rising customer expectations (shipowners, freight forwarders, stevedores), SOGETRAP must adapt its management approach to improve productivity and service quality.
To strengthen the effectiveness of docker management and contribute to the overall performance of the Port of Nouakchott, SOGETRAP is working on several strategic levers:
1. Professionalization and continuous training to enhance docker skills and adaptability
• Implement continuous training programs (safety, handling, logistics, use of modern equipment, etc.).
• Establish an in-house port training center in partnership with specialized institutions.
• Encourage professional certifications (STCW, ISPS Code, etc.) to increase employability and individual performance.
2. Human resources optimization to align workforce levels with actual port traffic needs
• Develop dynamic work planning (assigning dockers according to skills and workload).
• Use computerized personnel management systems (HR software, digital scheduling) to track productivity, absences, and skill development.
• Implement regular individual and collective performance evaluations.
3. Improvement of working conditions to motivate dockers and reduce accident risks
• Renovate infrastructure and work equipment (sanitary facilities, changing rooms, safety equipment, etc.).
• Provide adequate social coverage (health, retirement, work accident insurance).
• Promote a safety culture and responsible behavior through regular campaigns.
4. Social dialogue and participatory governance to foster a climate of trust and collaboration
• Strengthen communication channels between management and dockers (election of representatives, joint committees, regular meetings, satisfaction surveys).
• Ensure fair representation of dockers in decisions related to workforce management.
• Prevent social conflicts by setting up an internal mediation unit.
5. Technological integration and innovation to achieve greater operational efficiency
• Introduce digital tools to monitor schedules, absences, training, and assignments.
• Train dockers in the use of new technologies (e.g., tablets for cargo management, RFID scanners).
• Encourage reasonable automation of port operations while supporting workforce transition.